Welcome to the AG Glass Cover product page of SZ ClariTech Co., Ltd. We are committed to providing high-quality, stable etched AG glass covers for various industries, covering sizes from 1 to 32 inches.
AG glass (Anti-Glare Glass) is glass that reduces reflection and glare through the formation of fine concave and convex particles on its surface. This treatment roughens the glass surface, scattering incident light, reducing specular reflection, minimizing ambient light interference, enhancing screen clarity, reducing screen reflections, making images clearer and more realistic, and providing viewers with a better visual experience.
Our AG cover glass can be customized with a gloss range from 30° to 110°, available in both single-sided and double-sided treatments. This makes it particularly suitable for frame bonding processes, with gloss unaffected.
Gloss Application Fields
Thickness Option
We offer AG cover glass in various thickness specifications, suitable for different applications.
Differences Between Single-Sided and Double-Sided AG
Single-Sided AG: Gloss remains unchanged after lamination, suitable for full lamination, maintaining anti-glare effects.
Double-Sided AG: After lamination, the AG side is filled with OCA optical adhesive, losing its anti-glare effect while the other side takes over, increasing gloss by 10% to 20%.
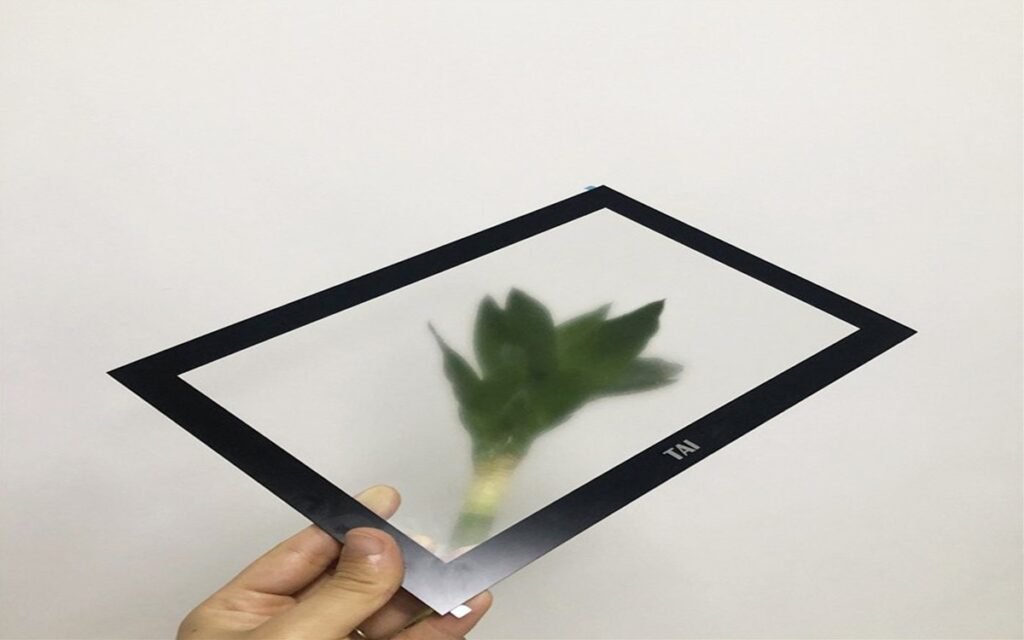
Touch Method
The AG side has an etching depth of 0.06~0.08mm, making it smooth to touch with a paper-like feel.
Observation Method
The AG side, treated with acid etching, has an uneven surface that blurs reflected images, while the untreated glass side reflects images clearly like a mirror.

Comparison between AG Glass and Regular Glass
Anti-Glare Effect: AG glass reduces reflected light and glare through special treatment, while regular glass easily produces reflections and glare.
Future Prospects of AG Glass
With continuous technological advancements and increasing market demand, AG glass has a broad application prospect in various fields. Particularly in smart devices, industrial control, medical equipment, and automotive displays, AG glass, with its superior performance, is gradually becoming the mainstream choice in the market.
Two Types of AG Glass Processing
AG glass not only has an anti-glare effect but also excellent scratch resistance 7H. This allowing AG glass to resist minor scratches and abrasions in daily use. For example, Corning Gorilla Glass has scratch resistance four times higher than ordinary aluminosilicate glass.
Common Issues with AG Glass in the Market
Solutions and Preventive Measure
Cost Comparison of AG Glass
Cost Differences
Key Quality Indicators to Consider When Choosing AG Cover Glass
When selecting AG cover glass, several key quality indicators should be considered to ensure you get a product that meets your needs:
Usually, glossiness is selected as a quality indicator, but it is best to combine this with an evaluation of physical samples to help you choose AG cover glass that meets quality requirements.
Applications of AG Glass
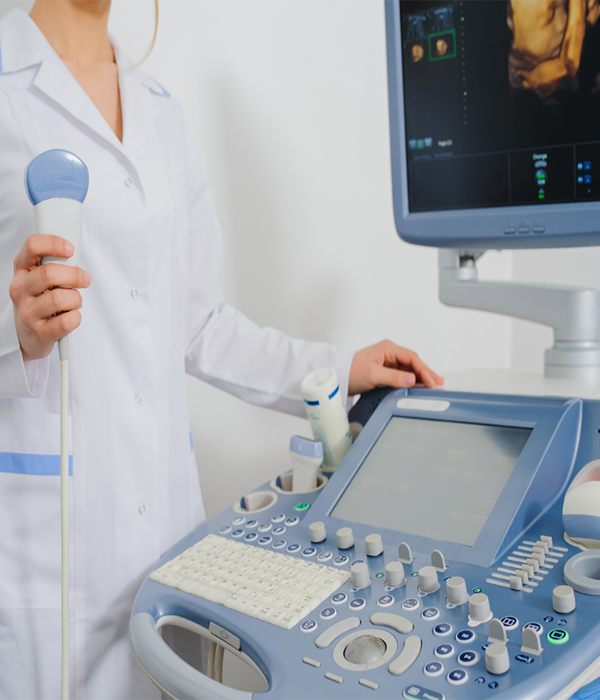